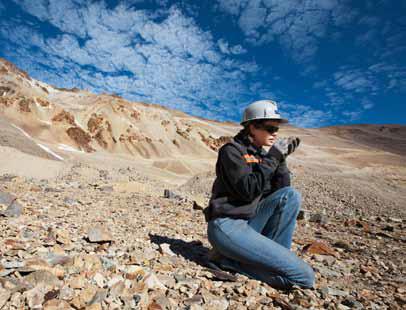
It may not be quite the highest mine in the world, but Los Bronces in the Chilean Andes has its own set of challenges for its new general manager Sam Rasmussen, as Alan Swaby learns.
Readers of this publication will be long familiar with arduous mining ventures. Normally, this means somewhere miles from nowhere in some hard to reach corner of the country. But in the case of one of the richest copper mines in the world, all the challenges and feelings of remoteness stem from the fact that it lies some 11,000ft above sea level.
“The Andes are practically on the doorstep,” says Sam Rasmussen, general manager of Anglo American’s Los Bronces mine, “and they create a wonderful backdrop to life in the city. The mine is only some 65km from Chile’s capital Santiago and just around the corner from one of the country’s skiing playgrounds. But working at about 3,500m, with several meters of snow a year, is challenging in anybody’s book.”
Not that the location has ever been a complete barrier to mining. As long ago as 1867, prospectors took their picks and shovels up the mountain to stake out a claim to the riches up there. So antagonistic did the rush for glory become that the area became known as La Disputada de Las Condes, with fights frequent and life cheap. Anglo American has been operating in Chile since 1980 and over the years has strengthened its holding through a series of acquisitions until, in 2002, it added the Los Bronces mine to its operations.
Los Bronces is an open-cut copper and molybdenum mine. In 2011, Los Bronces produced 221,762 tonnes of fine copper, including high-purity cathodes and copper concentrate, as well as 948 tonnes of molybdenum concentrate. In November 2007 the board approved an expansion plan aimed at increasing the mine’s annual copper output by some 278,000 tonnes in its first three years and by around 200,000 in the first 10 years. Molybdenum output is expected to rise to some 5,400 tonnes annually. With a total startup capex of US$2.8 billion, the project produced its first concentrate in November 2011.
But shortly after construction began the 2008 global recession started to bite and while work never actually stopped, it did slow down – making a project that would normally take about three years spin out to just under four to start producing. Rasmussen’s job is to iron out the wrinkles and ramp the plant up to production capacity. “Even though we are dealing with the same ore,” explains Rasmussen, “there is always a long period of fine adjustments necessary and a slow build-up of volumes to give the production team chance to spot potential problems. This is necessary because once up to speed, the new grinding facility in the Confluencia sector will have to process 87,000 tonnes of ore a day.”
In many ways, production at Los Bronces is very traditional. It’s an open-pit mine where ore is transported by truck to a bank of two crushers – one old plus one new installation – and later by conveyer to grinding facilities, for a total processing capacity of 148,000 tonnes per day.
The new SAG mill (of 12.2m x 7.6m) uses the latest gearless drive technology, where the axis of the mill is mounted with induction windings and becomes the motor drive rotor; but this in itself is very much proven technology rather than experimental. Nevertheless, the grinders bristle with sensors and circuits to control speed, flow and lubrication.
At its peak of output, Los Bronces will become the fifth largest copper mine in the world. Based on the latest expansions, despite having mined there for the best part of 150 years, Anglo American estimates the mine will be productive for roughly a further 30 years whether or not further deposits are discovered.
Perhaps the most novel aspect of the whole Los Bronces project is the way that slurry is transported to the Las Tórtolas flotation plant, where copper and molybdenum concentrates are produced. “There is no real problem crushing the rock at the altitude we do,” says Rasmussen, “but the separation process involves water and tailings. With so much of the time spent at freezing temperature and below, anything that relies on free access to water is going to be a stop/start process at some 3,500m.”
Therefore, the slurry (produced from ore ground at both the new and old grinding plants) goes on a roughly 54km ride down two pipelines to the valley below, where concentration facilities are located. Due to the force of gravity with which the slurry travels from grinding facilities at an altitude of some 3,500m to about 750m above sea level (the latter being the altitude of Las Tórtolas’ two flotation plants where copper concentrate is finally produced) five choke stations were installed along the pipeline route to slow the speed at which the slurry travels.
A key part of the initial project evaluation process was an environmental impact study. This was carried out in 2006 and approved by the Chilean National Environmental Agency the following year. It considers the use of areas intervened to date and therefore does not affect other environmental assets. Most of the additional water needed for the new grinding plant comes from greater recirculation from the Las Tórtolas tailings dam to the mine. In comparison to the older mills, the new set-up is much more water efficient and the quantity of fresh water used per tonne of copper produced will therefore drop by an estimated 25 percent.
Being on the side of a mountain means that there isn’t much space to spare. In fact, one of the biggest constraints Rasmussen has is working in such a confined space. “Effectively we are digging two pits,” he says, “although at some stage the ore bodies will merge and things will open up a bit more. Then, because of the number of snowy days we get, we have to maintain a sizable stock pile of ore to keep the crushers running during days when mining can’t take place.”
The one good aspect of Los Bronces’ location is that it is possible to commute if you are inclined to negotiate the mountain road on a daily basis. Rasmussen and some of the other managers usually take this option but for the majority of the 3,300-person workforce (roughly 50/50 staff and contractors) who work various shift patterns, daily life means staying at the Anglo hotel during the working week.
Los Bronces is just one of five operations Anglo American operates in four regions of the country with shareholding in a sixth, all managed from a head office in Santiago. In fact, Anglo American is one of the most important copper producers in Chile. Its vertically integrated structure means the Group covers every aspect of the process internally - exploration, mining, processing and marketing of copper cathodes, anodes, blister and concentrates, molybdenum concentrate and sulfuric acid.
Once, safety in the mining business was treated in a cavalier manner – and still is in some parts of the world. But for an organization such as Anglo American, where any incidents that do occur are highlighted in the company’s annual report, safe working conditions are uppermost in everyone’s mind. “Managers are all held accountable for the safety of workers,” says Rasmussen. “It is expected that all supervisors must provide effective leadership on safety for those who report to them, and acknowledge that good safety conduct is the responsibility of everybody working in the company. It’s their job to make technical inspections in each work unit to identify places and personnel with the highest risk exposure.”
Being such an important part of the Chilean economy, Anglo American recognizes and honors its social responsibilities. Over the years, the company has developed its own methodology, in conjunction with an environmental consultant, on how best to identify, assess and manage the impacts of its operations on the surrounding communities. It uses what is known internally as the ‘Socio-Economic Assessment Toolbox’ (SEAT) which helps identify the major issues in communities in the vicinity of mining operations and proposes efficient responses to their development. In fact, in 2004, the Casa de la Paz Foundation applied SEAT to all five operations in Chile, making it the first company within the Anglo American group to deploy this methodology across the board.
Since 2006, Anglo American has been running the ‘Emerge’ program, inspired by its experience in South Africa in 1980. The aim is to contribute to the economic development of communities near its operations by encouraging individuals to start their own commercial activities and to help existing small and medium-sized businesses to improve their performance. The scheme uses a mix of financial support and business development training and is currently operating in a dozen parts of the country. “The Emerge Program,” says Rasmussen, “aims to give communities the tools needed to kick start new businesses which not only support the entrepreneurs themselves but also create wider employment opportunities.”
A key component of this program is the strategic partnership Anglo American has with Fondo Esperanza, an institution which grants micro-credits and provides business education to community banks or groups of 18 to 25 people who live in the same area and come together for mutual support. In each community bank, members must serve as co-guarantors, committing to pay back the loan. So if one defaults, the others must step in and make up the shortfall.
Other more conventional aid programs are also undertaken, such as work to eliminate shanty towns or the backing of organizations devoted to improving educational opportunities. Back at Los Bronces, though, with the Southern hemisphere winter just around the corner, Rasmussen and his team are pleased with the progress that is being made with the new installations constructed with the expansion, which is nearing the end of its first six months of working life and on target to meet production schedules.
DOWNLOAD
AngloA-AM-May12-Bro-s.pdf